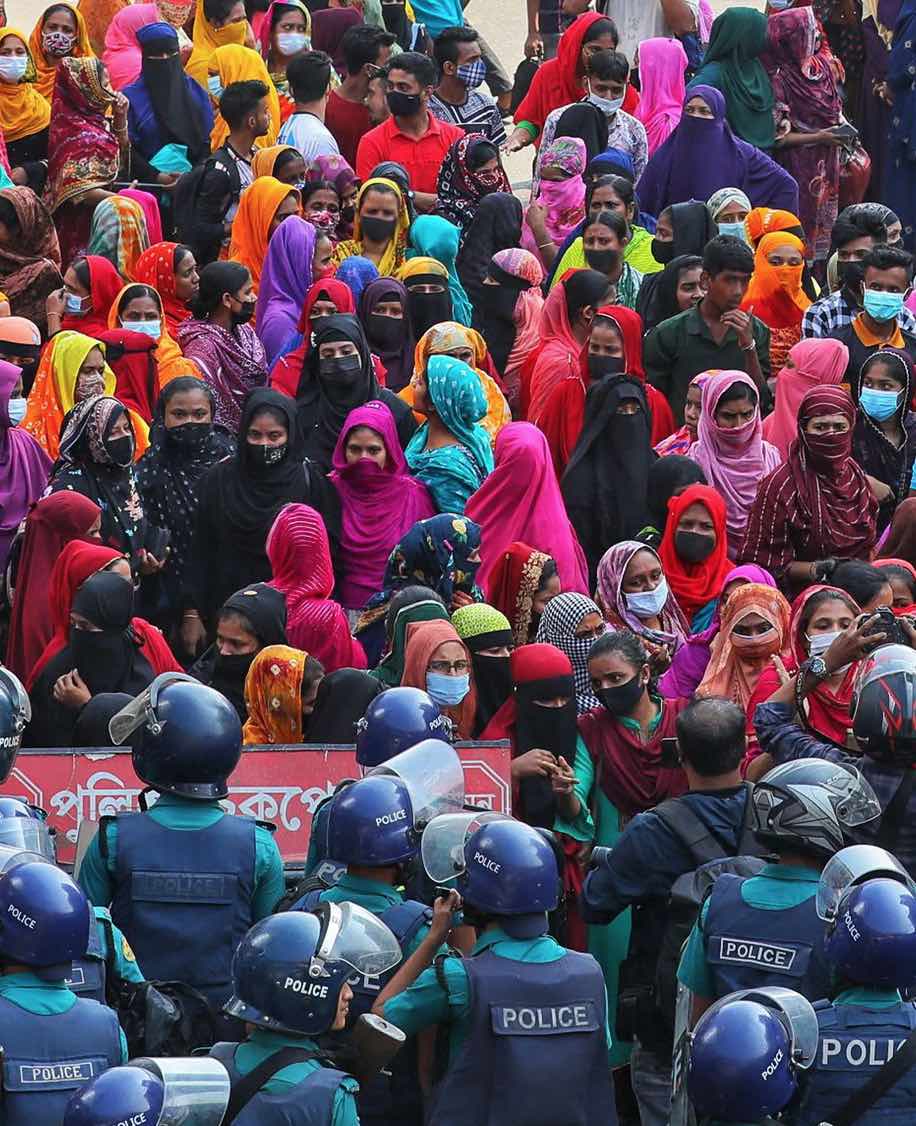
Poverty wages. Long working hours and uncompensated overtime. Health and safety risks. Workplace harassment and gender-based violence. Crackdowns on freedom of association. Conditions for garment workers have never been good, but increased transparency and a legislative push for due diligence is casting light on just how bad things have become.
Next week, non-profit organisation Business & Human Rights Resource Centre (BHRRC) will launch an initiative dubbed ‘Who Pays for the Crisis?’, publishing information on supply chain shocks that impact working conditions, and calling on brands to share their subsequent actions. The aim is to shine a light on how regularly issues arise that can lead to an erosion of workers’ rights and the role of brands — and ultimately raise awareness of the need for system-wide change.
“There are persistent, pervasive problems due to the structural inequalities baked into fashion supply chains and the industry more generally. It’s incredibly difficult to take a piecemeal approach to supply chains if that structural approach isn’t changing,” says Natalie Swan, labour rights programme manager at BHRRC. “You could have the most perfect due diligence process in the world, but if you’re not paying for human rights, you’re not going to see the mitigation of human rights risks along your supply chain.”
While there is a shared roadmap emerging, each garment-producing country has its own specific geopolitical conditions, which brands need to bear in mind before barrelling in to change things. Here, labour leaders in Myanmar, the Philippines, China and Bangladesh — four leading garment-producing countries that have appeared in the news recently for their treatment of garment workers — share their insights into the changes and challenges brands need to know about to build better supply chains.
Myanmar
Workers are struggling in Myanmar for reasons far beyond what fashion can control. Political instability has all but erased progress that workers had been making in recent years, ever since Myanmar emerged from a dictatorship in 2015, explains Christina Hajagos-Clausen, director for the textile and garment industry at IndustriAll Global Union. “They negotiated the first-ever minimum wage in the country; they set up a freedom of association protocol with global brands and suppliers, which had a commitment to move to sectoral bargaining; they established a complaints mechanism and a dispute-resolution mechanism. Then came the military coup in 2021 and the whole system fell apart,” says Hajagos-Clausen.
Since the coup, conditions have become untenable, says Khaing Zar Aung, treasurer of the Confederation of Trade Unions Myanmar (CTUM) and president of the Industrial Workers’ Federation of Myanmar (IWFM). She says the minimum wage has plummeted in value because of inflation, with many workers facing daily abuse and most of Myanmar’s union organisers are in hiding after continuous violence and arrests.
“There is an unholy alliance between garment factory employers and the military,” explains Andrew Tillett-Saks, organising director of Solidarity Center. Many brands have pledged to leave Myanmar, but in reality have not. According to Yangon-based news outlet Myanmar Labour News, conditions have only worsened since brands began announcing their often open-ended departures. The organisation recorded 455 incidents in 2023, three times as many as the year prior.
Trade union leaders in Myanmar are clear that they want international brands to leave the country immediately — because they want to “fight for the dignified jobs and democracy they deserve, not just the crumbs of brutal sweatshop jobs under a brutal military dictatorship”, says Tillett-Saks. There’s no way to operate responsibly, so any brand that maintains production in the country is complicit in the problem, they say. “Brands need to stop pretending to customers that they are doing due diligence in Myanmar. That is a lie,” says Khaing Zar Aung. “There is no way to do due diligence in Myanmar because the industries are under martial law.”
The Philippines
In the Philippines, garment workers have become collateral damage in China’s forced labour scandal. Sonny Matula, national president of the Federation of Free Workers, says he is aware of at least nine factories affected by layoffs off the back of the US crackdown on Xinjiang cotton linked to forced labour through its Uyghur Forced Labour Prevention Act (UFLPA). Over 4,000 workers are said to have been retrenched, with a further 500 forced to go on leave.
This is just the latest in a string of external events that have set Filipino garment workers up for failure. In 1974, the Philippines joined the Multifiber Arrangement (MFA), which established quotas on the amount of clothing and textiles that developing countries could export to developed nations. When the MFA ended in 2005, the Philippines struggled to match the production capacity of its competitors, largely because it is reliant on imported textiles to fuel its garment-production industry. Government plans to revive the industry and promote indigenous raw materials such as abacá and ramie “never prospered”, explains Ramon Certeza, regional secretary for the South East Asia division of IndustriAll.
Now, the government’s historic failure to act is catching up with the garment sector. The Philippines remains dependant on imported raw materials, and the lack of clear data about where these come from is causing problems for garment manufacturers, who are facing increased pressure from brands to comply with incoming transparency and traceability regulations. As a result, those factories are struggling financially, exacerbating long-term issues with workers’ rights.
According to Certeza, union-busting is common in the Philippines, and factories often hire workers through external agencies, blurring the lines of responsibility and making it easier to terminate contracts. There are platforms for tripartite negotiations, but recent studies have shown that these are not translating into unionisation or collective bargaining agreements. In the meantime, workers face long working hours, insufficient wages and gender-related issues. “Without better data, things have become very challenging,” he says. “The last big textiles factory just recently closed, affecting more than 2,000 workers. The action plan has not been realised. The textile sector here is dead.
China
Workers’ rights in China have been a hot topic since 2020, following allegations of widespread human rights abuses and forced labour in cotton supply chains, particularly in the northwestern province of Xinjiang. But hearing from workers directly — and therefore finding solutions based in collective bargaining — is incredibly difficult. China essentially has a single trade union, the state-run All-China Federation of Trade Unions (ACFTU). “Workers in China have no bargaining power, no representation,” says Han Dongfang, director of China Labour Bulletin (CLB). “When bargaining power is ignored, and factories are scared to lose orders, they squeeze workers as low as possible. This is the core sickness of this industry.”
The problem is not Chinese labour law, says Dongfang. The problem is getting suppliers to abide by that law, and giving workers a means to report and rectify violations of it. “The union does not want to negotiate proper procedures or compensation for workers — that’s not in its DNA,” he explains. “So my organisation aims to do something impossible — bringing their inaction to light case by case. Hopefully our work creates pressure that makes them act.”
International pressure is also growing, underpinned by a wider anti-China sentiment. In the US, the UFLPA came into force in June 2022. US Customs and Border Protection has detained almost $2 billion worth of goods since. In France, legislators are attempting to ban fast fashion, taking particular aim at Chinese giants Shein and Temu. “We see the laws this way: as problematic but outside of our scope of consideration,” says Dongfang. “We will leverage anything available to give our workers a better life.”
Brands can help by paying factories more and supporting workers in their bid for bargaining power rather than deferring to empty promises about freedom of association in their code of conduct. “You can’t make the factory owners pay workers more if brands aren’t willing to pay more — factories are not charities,” adds Dongfang.
Key takeaway: With only one state-run union, China lacks meaningful worker representation, hindering collective bargaining efforts and progress on garment worker rights. Brands need to adapt their purchasing practices and pay factories more to enable the better treatment of workers.
Bangladesh
Bangladesh has been at the forefront of the conversation around garment workers’ rights since the Rana Plaza factory collapse in 2013, but progress remains slow, and the nature of unionisation is partly to blame.
While Bangladesh has relatively high rates of unionisation compared to other garment-producing countries, it is largely fragmented and fails to reflect worker demographics. Many unions are affiliated with a single factory or company, with very few independent, sector-wide unions. Despite the majority of garment workers being women, the International Labour Organisation says Bangladesh’s unions lack female membership and leadership, which impacts their approaches to gender-based issues such as maternity leave, sexual harassment and automation reducing the number of “women’s jobs” without upskilling to redirect their livelihoods. “This sector is dominated by women, but most of its unions are dominated by men. That needs to change,” says Nazma Akter, founder and president of Awaj Foundation and Sommilito Garments Sramik Federation.
Recent backlash against striking garment workers is another threat to unionisation. Bangladesh was in the hot seat at the end of last year, when months-long protests over the new minimum wage reached a violent crescendo. Four workers were killed, many more injured and hospitalised, and several hundred were arrested. Akter says there are still many workers on industry blacklists, struggling to get work after being fired for their involvement. Despite protests coming to an end, the struggle continues. “Inflation is very high, living costs are very expensive, and many workers cannot afford to live without wage increases. There is lots of inequality, widespread nutrition problems, and — with no childcare or creche on site — many workers have to send their children to the countryside.”
In response to this backlash, the American Apparel & Footwear Association (AAFA) sent an open letter to the Prime Minister of Bangladesh imploring the government to drop criminal charges and reinstate fired workers. Moving forward, Bangladeshi garment workers and their unions need more active international support to secure better rights and conditions, namely legally-binding agreements. “Freedom of association and collective bargaining, gender-based violence, living wages and social protections, and climate justice — these are big issues in Bangladesh. Brands are not asleep, they are awake to this, they know what is happening. This culture needs to stop.”
Key takeaway: Garment workers need trade unions that truly represent them, and the lack of gender diversity in Bangladeshi unions is holding back its mostly female workforce. With increasing legislative and consumer pressure on brands to share who made their clothes and in what conditions, that means an uphill battle for better conditions.
Where do we go from here?
The four countries highlighted above give a flavour of the complex issues garment workers face, but there are many more garment-producing countries with their own geopolitical contexts to consider. Despite many issues crossing country lines, a one-size-fits-all approach will never work, and brands will always need to consult with local labour leaders to achieve meaningful change…
Read more – Vogue Business